Meeting the challenges of the changing construction industry
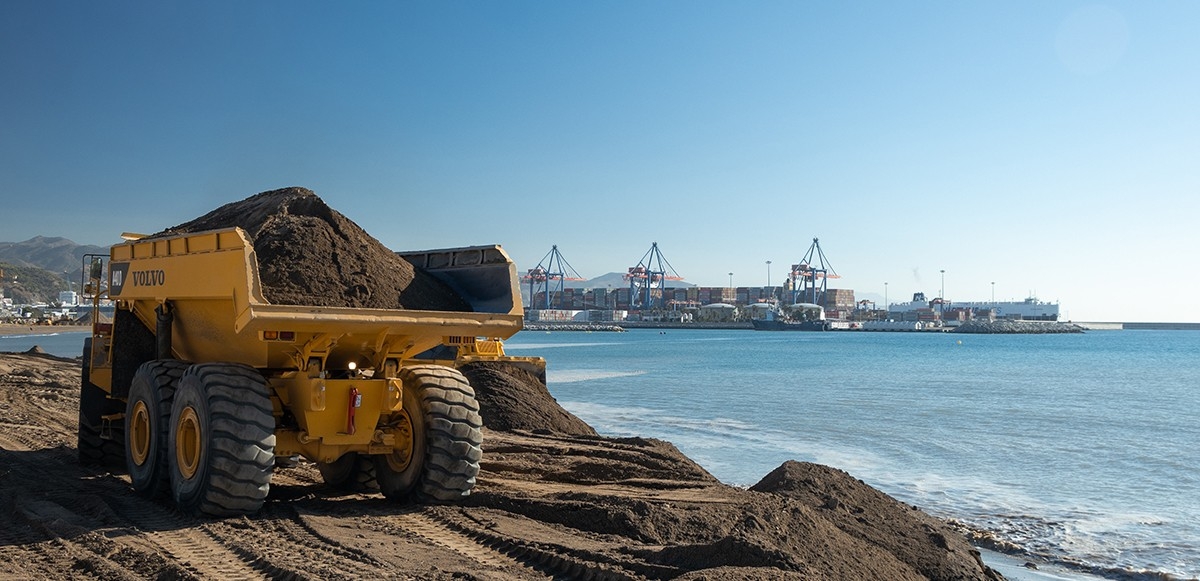
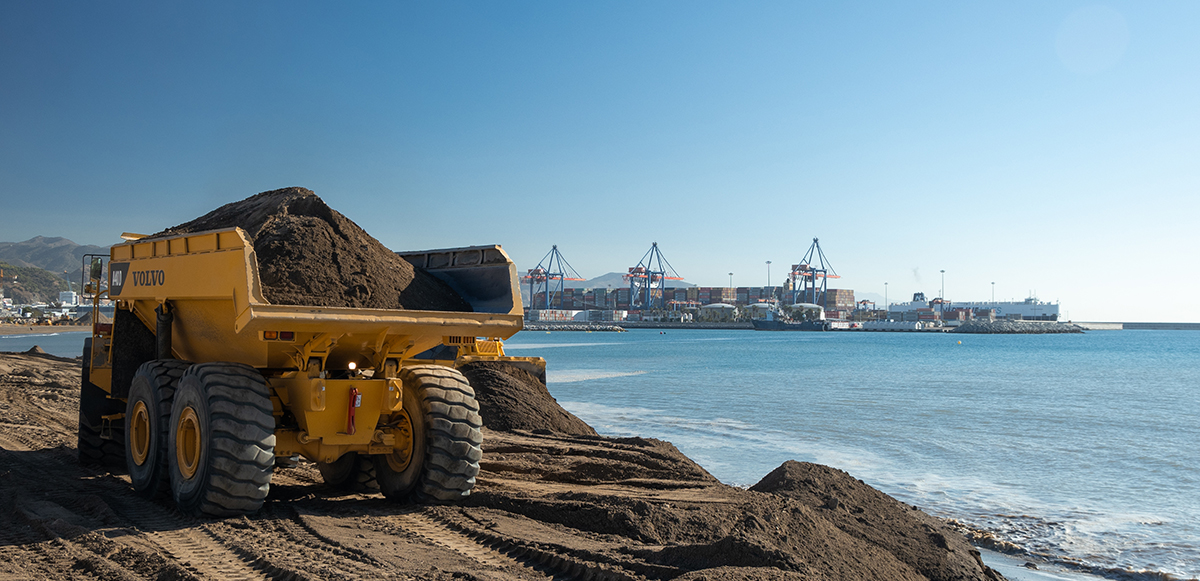
Construction equipment manufacturers face several concerns, including a continued call from customers and legislators for improved efficiency and productivity. This is combined with the constant desire to reduce total cost of ownership. The main drivers to achieve these seemingly incompatible objectives are connectivity, automation and digitalisation.
Equipment manufacturers faced further legislative changes with the adoption of Stage V emissions standards across Europe in 2019, resulting in further cuts in harmful exhaust emissions. EU Stage V standards were adopted across Europe in 2019 for engines below 56kW and above 130kW, with engines in the popular 56-130kW band conforming to the standard in 2020.
Stage V included a much wider group of engines and fuel types and bring many stationary applications, such as generators and crushing equipment, under the regulation.
In anticipation of this, many engine providers had already adopted diesel particulate filters (DPF), selective catalytic reduction (SCR) with a diesel exhaust fluid (DEF) additive such as AdBlue, plus cooled exhaust gas recirculation (EGR). All of these solutions often call for the use of specific oils and lubricants along with low sulphur fuels, to work with ultra-high-pressure fuel injection systems.
The need for extensive exhaust after-treatment has driven a growth in both exhaust systems and machine cooling packs, as many construction machines operate with minimal physical air movement.
Through the use of improved lubricants such as Texaco Delo, manufacturers have been able to extend service intervals, with most operated equipment now able to work for at least 500 hours between engine oil changes. Hydraulic filtration and improvements in oils has also led to oil change intervals of up to 5,000 hours, with filter changes now over 2,000 hours in many cases.
Even regular daily and weekly checks are being extended, with improved lubricants such as Texaco Delo, and impregnated bushes taking greasing times out to as far as 500 hours. This is particularly important for the rental industry, where operators can be less rigorous when observing regular maintenance schedules.
As construction machinery becomes increasingly sophisticated, the reliance on repair and maintenance (R&M) contracts is more common. With many contracts including regular sampling of engine, hydraulic, axle and transmission oils for analysis, frequent assessment of wear within the component or assembly is more common.
Such predictive maintenance allows dealers and machinery owners to access a wealth of information, helping ensure equipment durability, and avoid costly failures.
For further information about the Texaco Delo product range please visit: Texaco Delo products