Equipment Maintenance – Reactivity, Prevention or Prediction?
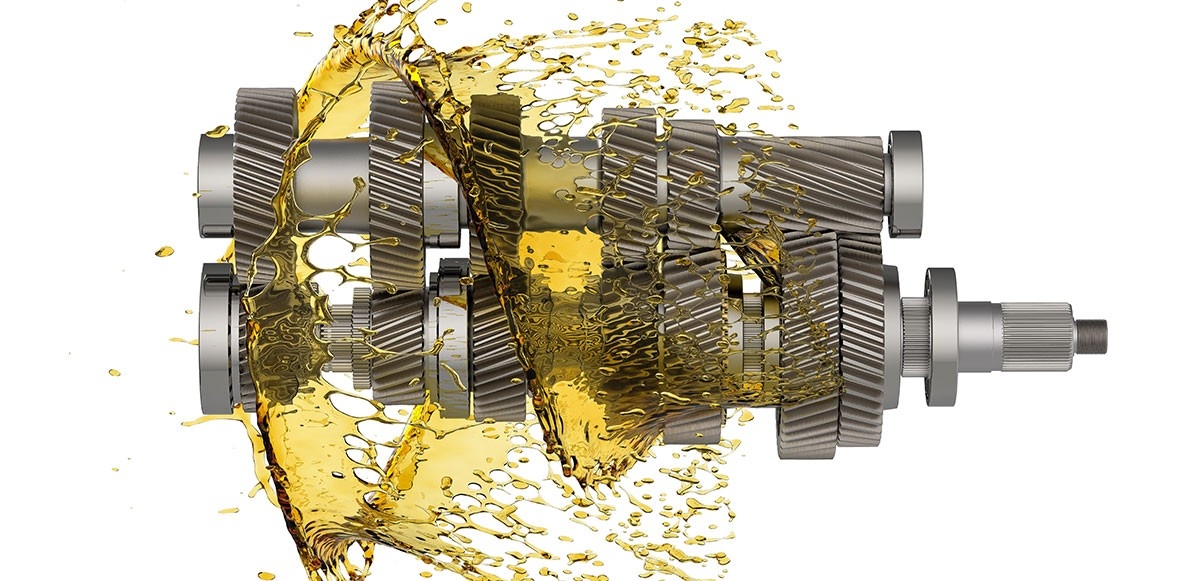
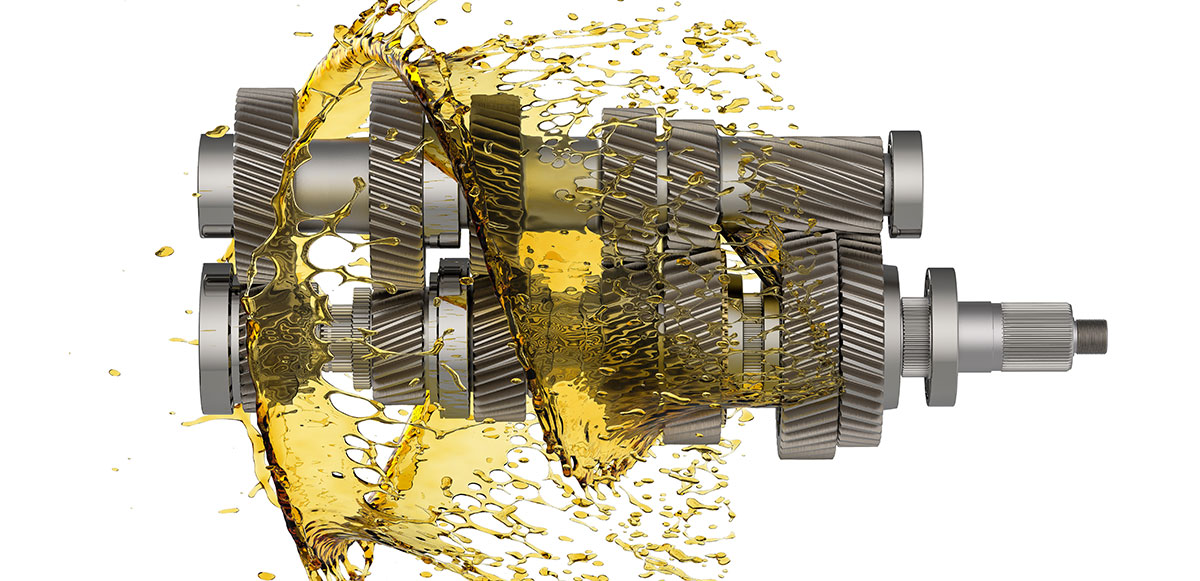
For many Texaco customers, equipment reliability is not just an ideal, but a vital part of their day-to-day operations. Whether you’re running on-highway transport, railway, inland marine, or power gen services, your business relies on equipment that is running consistently.
For some, reactive maintenance is still the norm. Engines and other critical equipment are kept running for as long as possible, even at less-than-optimal output, and maintenance is only performed when breakdown or loss of power necessitates intervention.
In recent years, businesses have understood that reactive maintenance is extremely inefficient and have embraced the benefits of a more preventative model. By ensuring that maintenance and service schedules are diarised regularly far in advance of any unexpected issues, concerns over unplanned downtime and lost income can be minimised.
But can the preventative model be improved upon? Many within companies such as Texaco Lubricants believe so. While prevention is by far a better philosophy, it can also have its drawbacks. Planning maintenance based on generic timescales or usage figures can lead to intervention too early in your operations, replacing parts, lubricants, or the equipment itself before it has reached full efficiency or the end of its useful life.
This is where the concept of predictive maintenance comes into play. Thanks to advances in technology and increased interconnectivity through the Internet of Things (IoT), companies are looking to adopt practices commonly described as part of the Fourth Industrial Revolution or Industry 4.0.
Industry 4.0 encourages companies to collate data from different sources to fully understand the condition of specific equipment in real time. This is, of course, challenging, accessing the right data and analysing the results is not always straightforward, but moving to a predictive maintenance model, means decisions can be based on current facts about your specific systems. This potentially leads to improvements in equipment performance, less unscheduled downtime, and allows operators to review performance data in conjunction with other business factors such as demand forecasts or production schedules.
So, how does Texaco Lubricants help support predictive maintenance best practice? Simply put, the Texaco LubeWatch oil analysis programme can help equipment run better for longer. Research undertaken by Polaris for the oil analysis industry* showed that 80% of users were able to maximise their equipment uptime thanks to oil analysis, while 69% had used their analysis results to optimise oil drain intervals by up to two times that of the standard drain (something those running preventative maintenance are unlikely to do). Finally, the research also concluded that 80% of customers using oil analysis reported that scheduled downtime based on their results saved money compared to the cost of unexpected equipment failures.
Through regular oil analysis, LubeWatch enables you to track the performance of vehicles and equipment so that oil replacement intervals can be optimised, lubricant needs can be identified, and the changing environment within the equipment can be monitored.
However, completing the analysis is only the first step towards full integration of the data. To fully embrace predictive maintenance and prove the value of the oil analysis programme, it is vital to consider integrating the analysis directly into your asset management system via a tool such as DataConnect. DataConnect allows the seamless import of sampling data into your existing computerised maintenance management system (CMMS) or enterprise resource planning (ERP) system to provide a more integrated overview of your operational efficiency.
Guus Volkstedt, Field Technical Manager – Europe, commented “Tight operating margins and competitive markets have significant impact for our customers. Our aim is to provide the products, services, and expertise to help them maximise their business potential. The concept of predictive maintenance is not a new one, but crucial with operational efficiency. The time is right for many more companies to investigate how it could work for them. Data-driven knowledge can give you the edge to reduce downtime, potentially lower costs and improve business productivity.”
*POLARIS OUTLOOK 2015 Benchmark Study for the Oil Analysis Industry.