Industrial Gear Oils Q&A
In conversation with Johan Luycx, Texaco Product Technical Support Specialist Europe
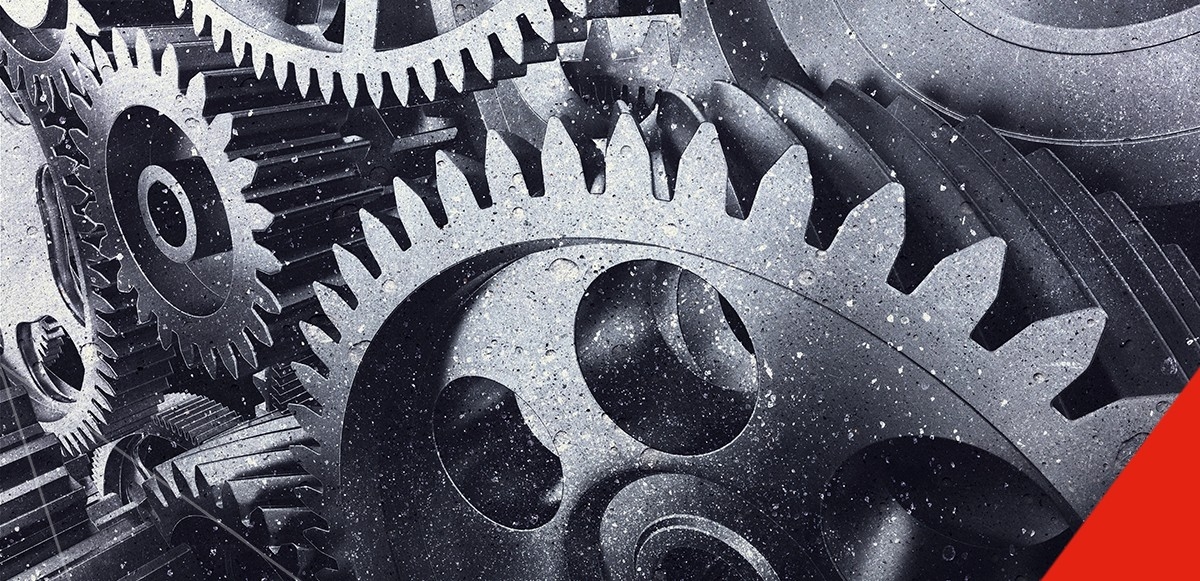
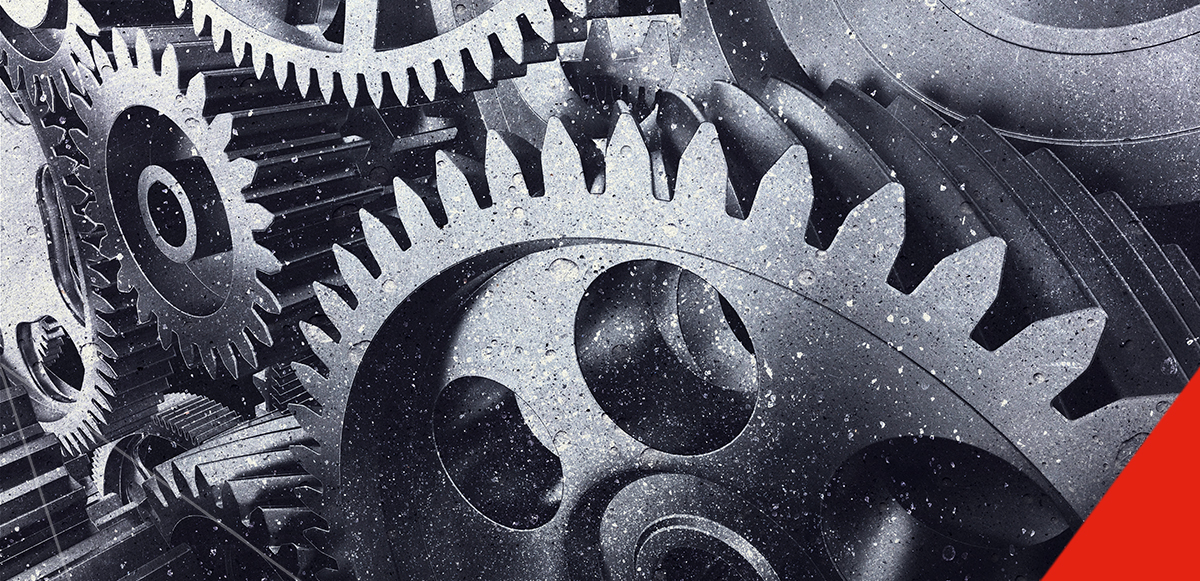
What are the key properties of a gear oil?
In today’s industrial environment, equipment is being pushed to work faster and harder than ever before. Customers and service providers are therefore looking for ways to boost reliability, minimise downtime and optimise performance across their operations.
Gear oil reliability can be key in many different applications, but manufacturers of these specialist lubricants have a lot of requirements to take into consideration. This includes areas such as filterability/compatibility of seals and coatings, protection against micro pitting, bearing protection, cold temperature performance, oxidation, and varnish control.
Additionally, gear oils need to meet global industry standards, individual OEM (Original Equipment Manufacturer) approval requirements and be assessed against FZG testing. FZG stands for, Forschungsstelle fur Zahnrader und Getriebebau, and is the evaluation recommended by the Technical Institute for the Study of Gears and Drive Mechanisms, which evaluates fluid lubrication and wear protection properties at the interface of a loaded set of gears.
What do you believe are the key trends in industrial gear oils currently?
There are three key trends in the sector currently, energy efficiency, transmission of power and reliability. Each of these areas is important to operational performance, but lubricant manufacturers must also consider the effects of these requirements on the oil itself. The viscosity of the oil must remain stable, with consistent high shear stability and oxidation resistance. When you also factor in the desire for longer oil service life and extended drain intervals, lubricant manufacturers have highly complex needs to balance.
How have specifications around industrial gear oils changed in recent years?
There are differing requirements dependent on the application, but it would be fair to say that across the board, complexity is growing.
For example, wind gears require gear oils to provide longer life capability and increased robustness. This is the case particularly around white etching cracking (WEC), which is a major cause of bearing failures in wind turbines and of course, the oils must have high-level varnish performance. Marine gears put a high focus on overall gear performance, with a particular emphasis on multi-disc clutch friction performance. Geared motors require high levels of dynamic sealing compatibility function, while precision gears, adapted for use in robotics and machine tools need strong anti-wear characteristics and critical bearing reliability.
How can customers save on energy usage?
It sounds simple, but it is important to ensure you have the right viscosity. When the oil film is too thin, you risk metal on metal contact, but if the oil is too thick you lose energy. Even in a gear box that is running at constant speed and load, the different components in the gear box run at different speeds and need different viscosities.
The viscosity of an oil changes according to fluctuations in the machinery operating temperature, so you might need to select a product with a high viscosity index. Switching from a mineral gear oil of the same viscosity to a synthetic or semi-synthetic gear oil can potentially help to improve energy savings.
What advice would you give customers to enable them to get the best out of their gear oils?
First and foremost, I would recommend customers always follow guidance from the OEM and the lubricant supplier. Texaco, for example, has extensive European resources both in base oil production and additive capabilities. We conduct regular proof of performance trials in partnership with OEMs and customers and can advise on areas of operational performance.
To get the best performance and reliability from your equipment, I’d also highly recommend using a system, such as Texaco’s LubeWatch Oil Analysis programme. Taking regular oil samples for analysis will provide a clearer view of your equipment’s performance and productivity. This allows operators to plan maintenance intervals when it suits the business and helps to minimise potentially costly and unexpected downtime.
Click for further information about Texaco Meropa high performance, multipurpose gear lubricants .