Removing Varnish from Turbines and Centrifugal Compressors Part 2
VARTECH® System Cleaner Launch Technical Q and A
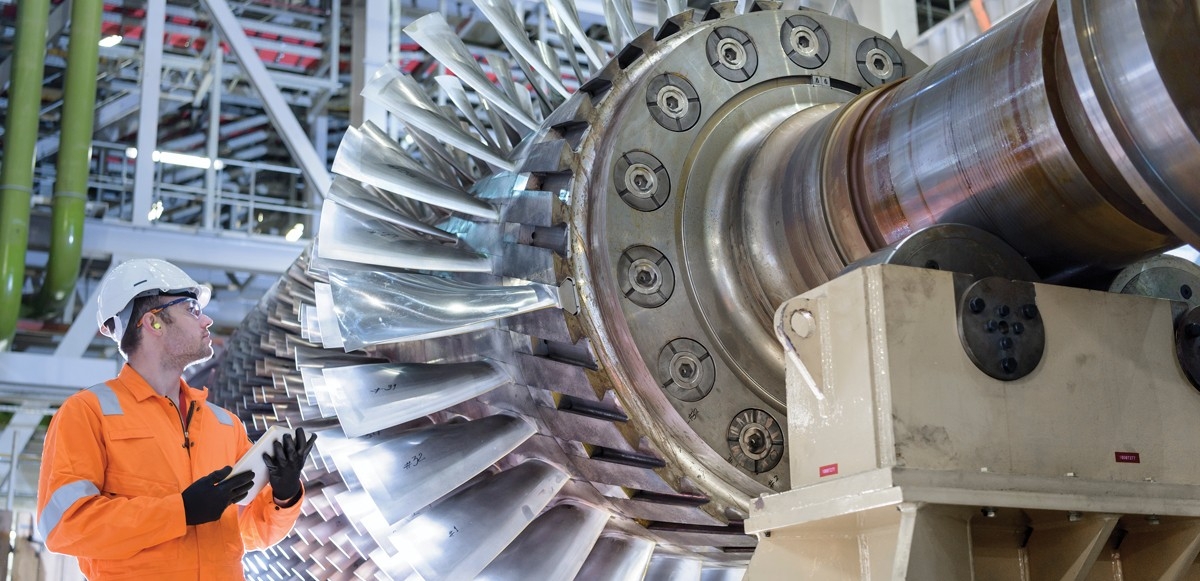
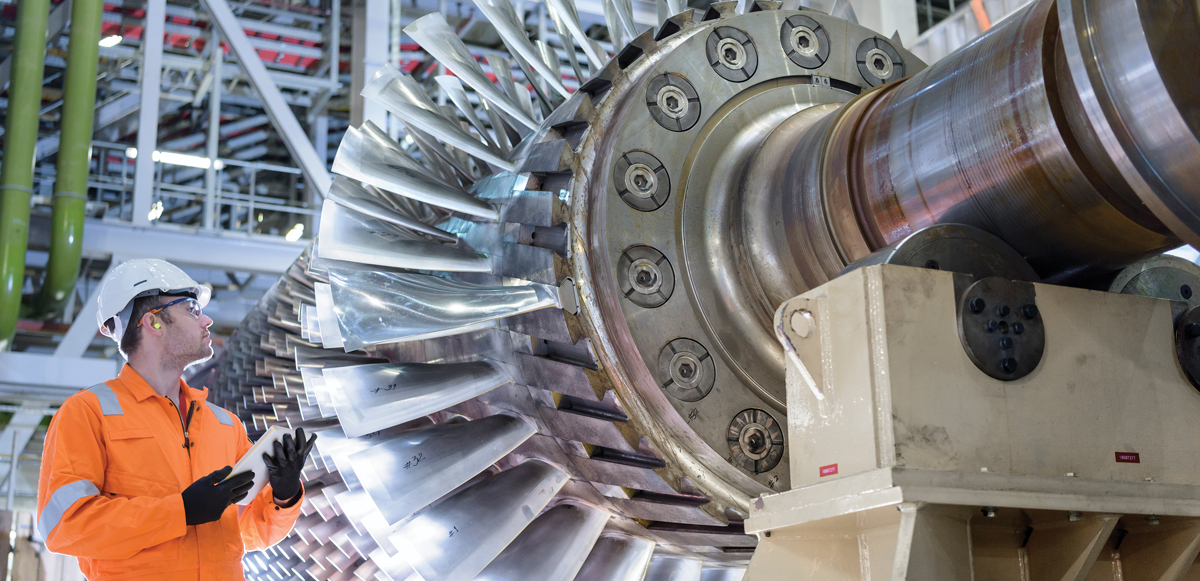
Background
Varnish is a common issue in circulating oil systems. It can cause huge operational problems and can cost businesses millions of dollars. Even the smallest amount of varnish in a system can result in erratic component operation such as valve sticking, poor heat exchanger performance and even bearing failure. These problems also lead to a shortened oil life and loss of equipment productivity.
Ways to mitigate varnish problems have consequently received much attention. Various methods have been used but most start with removing accumulated varnish from the oil system before implementing prevention and control methods. The most commonly used method for removing varnish from circulating oil systems such as turbines and compressors involves the temporary addition of cleaning chemicals to the system.
Q. Why should I clean varnish from my system? Paul Sly:
Varnish affects both machine operation and the performance of newly installed oil. Removing varnish often restores machine operation, efficiency and prepares a system for better performance after an oil change.
Q. How will the cleaner affect how I operate my system? Paul Sly:
A. Most equipment can be used in normal operation while the cleaner is in the system. After the cleaner is added to the existing oil, operating parameters should be watched to:
- Identify evidence of cleaning success, such as temperature changes, flow improvements and visual deposit removal
- Watch for filters that need to be changed (some cleaners are prone to plugging filters)
Q. Why should I drain effectively before refilling with fresh oil? Paul Sly:
A. Old, degraded oil mixed into the refill oil will diminish the performance of the fresh oil. Residual cleaner will affect both the performance and life of the fresh oil. Some alternative cleaners are so incompatible with fresh oil that they can reduce the expected life of the oil by ⅔ based on Rotating Pressure Vessel Oxidation Test (RPVOT) tests.
VARTECH Industrial System Cleaner is specifically formulated to be compatible with most turbine oils and so help minimise the impact of residual cleaner on the fresh oil.
Q. Do I have to rinse flush after cleaning? Paul Sly:
Rinse flushing is best practice for any oil change to completely remove old, degraded oil from all parts of the system, particularly when any of the following conditions exist:
- Prior to cleaning, the in-service oil was experiencing rapid oil degradation or was extremely degraded
- Prior to cleaning, there were severe deposits in the system
- More than 10% of the oil-cleaner mixture remains after draining
Complete draining of all the old oil and cleaner mixture, including trapped mixture, helps mitigate the negative impacts on new oil performance and can reduce the need for flushing.
VARTECH Industrial System Cleaner was formulated to be highly compatible with modern high-quality lubricants to help minimise the risks of an incomplete drain or rinse.
Q. Can I use the cleaner myself or do I need a service provider? Paul Sly:
A. That depends on the complexity of your system and the capabilities of your team. Simply adding the cleaner, operating the system, and then performing a thorough oil change can be an effective approach. A service provider often brings valuable experience and can be very beneficial in confined space entry for reservoir wipe down, certified oil disposal, filter changes, and providing auxiliary heat for offline cleaning. They can also aid in determining cleaner residence durations and application concentrations.
Q. How do I know if the cleaner has worked? Paul Sly:
Evidence can be found in several areas although not all of these will apply to every system:
- Reduced temperature across oil coolers
- Lower bearing temperatures
- Reduced valve sticking or delayed actuation (hysteresis)
- Reduced vibration
- Visual observation of reduced deposits
- Darkening oil color
- Membrane Patch Colorimetry (MPC) will often lower immediately and stay very low during the cleaning as the insoluble varnish precursors which register on the MPC remain stabilised in the oil
- Captured debris in filters
- Used Oil Analysis
Q. How long will my system stay clean after I clean it? Paul Sly:
That depends on whether the root cause of oil degradation has been addressed. Identifying and eliminating the root cause of oil degradation specific to your system will greatly improve oil life and system cleanliness. Your system will stay cleaner for longer if you correct system problems that damage oil and refill with a high quality, varnish-resistant oil.
Q. How often should I use the cleaner? Paul Sly:
Many operators choose to use a chemical cleaner as part of every oil change process. Others choose to clean only when operational evidence of varnish deposits are present. Deliberate consideration of whether to clean or not should form part of the planning for every oil change.
Q. Can I add VARTECH Industrial System Cleaner to a lubricant to make it a varnish resistant oil? Nathan Knotts:
No, Texaco lubricants with VARTECH technology are specially formulated to incorporate varnish controlling properties into the lubricant. VARTECH Industrial System Cleaner is designed to clean systems and uses different formulations.
Q. Can I use VARTECH Industrial System Cleaner as a top-treat life-extender? Nathan Knotts:
Texaco does not recommend this approach as:
- Modern lubricants are high performing advanced technology formulations and the chemicals in the cleaner can adversely alter the balance of the formulation which may in turn cause unexpected lubricant upset over time
- Varnish and other contaminant particles remain in the system until removed with the oil
VARTECH Industrial System Cleaner is designed as an end-of-oil-life cleaner precisely to help avoid these issues. Its components are not tailored for long periods of operation such as the multiple years turbine oil is often in service.
Q. Can I use VARTECH Industrial System Cleaner in non-turbine applications? Paul Sly:
VARTECH Industrial System Cleaner is recommended and has been tested in centrifugal- and screw compressors.
- VARTECH Industrial System Cleaner is intended for use in mineral and PAO synthetic oils but not in exotic synthetic chemical lubricants such as PAG, POE, or diester fluids
- Flooded screw compressors are used with a wide variety of gasses, not all of which have been tested so results may vary depending on the process gas
- VARTECH Industrial System Cleaner is not ideal or recommended for reciprocating compressors as their varnish often occurs in valves which don’t get much oil contact. In addition, the lower viscosity (55 cSt) of VARTECH Industrial System Cleaner may lower the viscosity of the lubricant beyond OEM recommendations
The use of VARTECH Industrial System Cleaner in heat transfer systems is likely beneficial but testing and use instructions are not yet complete. VARTECH Industrial System Cleaner is not ideal or recommended for natural gas engines as their varnish often occurs on valve stems and guides which don’t get much oil flow, plus the lower viscosity (55 cSt) of VARTECH Industrial System Cleaner may lower the viscosity of the lubricant (usually 150 cSt) beyond OEM recommendations.
Texaco has not yet completed testing VARTECH Industrial System Cleaner in hydraulic systems.
Read more about VARTECH™ Industrial System Cleaner varnish remover.