Removing Varnish from Turbines and Centrifugal Compressors
VARTECH® System Cleaner Launch Technical Q and A
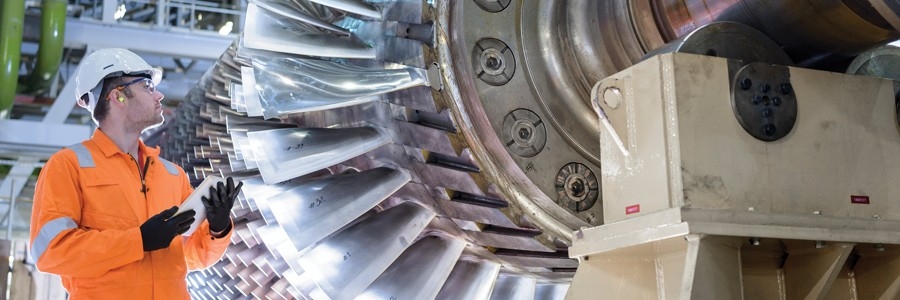
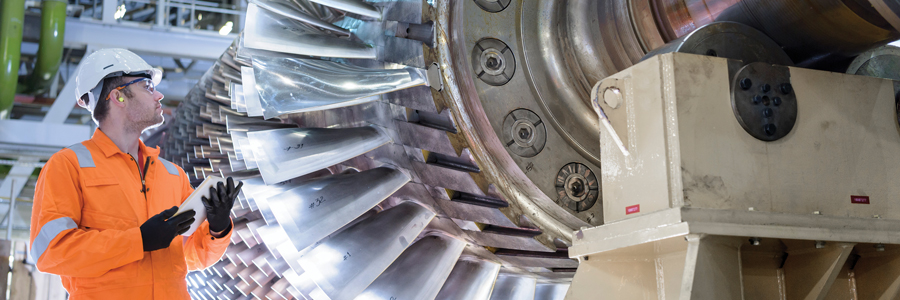
In discussion with Chevron Lubricants Specialists: Paul Sly, Global Industrial OEM Specialist and Nathan Knotts, Global Brand Technical Manager
Background
Varnish is a common issue in circulating oil systems. It can cause huge operational problems and can cost businesses millions of dollars. Even the smallest amount of varnish in a system can result in erratic component operation such as valve sticking, poor heat exchanger performance and even bearing failure. These problems also lead to a shortened oil life and loss of equipment productivity.
Ways to mitigate varnish problems have consequently received much attention. Various methods have been used but most start with removing accumulated varnish from the oil system before implementing prevention and control methods. The most commonly used method for removing varnish from circulating oil systems such as turbines and compressors involves the temporary addition of cleaning chemicals to the system.
What are the benefits of the new VARTECH Industrial System Cleaner?
- Is compatible with many in-service oils at the recommended concentrations of 5 - 20% by volume for the recommended cleaning durations (allowing longer residence times and generally removing the need for flushing)
- Causes minimal filter plugging
- Has very good seal compatibility
- Has shown superior deposit removal effectiveness in extensive comparative laboratory and field testing
- Is designed to dissolve varnish deposits from internal surfaces and then stabilise them for removal with the used oil
- Has a viscosity of 53 cSt which helps make it effective in ISO 32-68 viscosity oil as it will not significantly affect oil viscosity at the recommended concentrations
- Has a minimal impact on lubricant water separability
- Has minimal impact on long term new oil performance in residual amounts up to 2%
How do I know I have a varnish problem? Paul Sly:
Symptoms of varnish deposits vary even between identical systems. Typical symptoms include sticky servo or thermostatic valves, sticking hydraulic cylinders, inefficient oil coolers leading to high oil temperatures, high bearing temperatures, and subsynchronous vibration in high-speed bearings and seals.
What tests will definitively prove I have varnish? Paul Sly:
Oil analysis test methods fall broadly into two types: those that predict the life of the oil and those that measure the current performance of the oil. Note the key word ‘oil’. The first test type will only indicate the varnish potential of the oil. At best, the second test type will only indicate the amount of varnish and varnish precursors in the oil. Neither test type provides an indication of varnish deposits on equipment surfaces nor whether such deposits are problematic. Oil analysis is therefore merely suggestive with respect to confirming that a system’s performance issues are varnish related.
In addition, all oil analysis tests used for identifying varnish problems present challenges such as:
- The oil sample tested may not be representative of the oil in the whole system
- The potential for varnish may change through the year depending on system utilisation rates as degradation products often come out of solution to form deposits in an idle system
- Varnish precursors are difficult to measure as (a) they are very small (sometimes < 0.1μm) and (b) test methodologies measure only soft varnish precursors in suspension, but the precursors are oil-soluble and can easily move in and out of solution depending on sample handling
- As a proxy for varnish-potential which itself is a proxy for varnish deposition, tests measure the overall ‘health’ of the oil or the additive package or the amount of varnish precursors in the oil
There is no direct, definitive way of identifying varnish-related system issues that do not involve measuring critical parameters like valve hysteresis or oil cooler effectiveness or even tearing down the system to visually ascertain the root cause. Refer to the guide to Varnish Testing for more information.
How long can I keep the cleaner in my system? Paul Sly:
For most cleaners, the duration for effective cleaning is usually from 1 to 30 days. The longest VARTECH Industrial System cleaner has been tested in a system is five months.
Cleaners are designed to move varnish deposits from surfaces into the lubricant. Oil with these suspended contaminants is not as good a lubricant as fresh oil without them. It is best practice to change the oil once the cleaner has done its job.
Modern lubricants consist of high performing advanced technology. Since cleaners were not an original part of the oil formulation, long-term performance is hard to predict. Consideration should therefore be given to the likely actual long-term effect on lubricant performance by the cleaner remaining in the system.
How long should I keep VARTECH Industrial Cleaner in my system? Paul Sly:
Generally, the longer a cleaner is in a system, the more varnish is removed, up to a limit. Even with the best cleaner, there is a limit to how much varnish a severely degraded oil can absorb.
Will the cleaner remove all the varnish from my system? Paul Sly:
Removing every speck of varnish is unlikely. The varnish chemistry will vary throughout the system. Some chemistries like soft varnish in coolers and sludge in reservoir bottoms often clean quickly and completely. Hard, polymerized deposits or those containing contaminants can be very stubborn and may remain after cleaning.
Areas with low flow or low temperatures are unlikely to be completely cleaned, although a good cleaner will soften the varnish to ease manual removal.
Why shouldn’t I drain my system when cold? Paul Sly:
Varnish solubility in oil is very temperature dependent. Draining the oil while it is warm (safe handling temperatures) and recently circulated, ensures maximum removal of the varnish deposits that have been moved into the oil. Allowing the oil to cool and stagnate for more than a few hours can re-deposit some of the varnish on the walls of the equipment.
Why aren’t my reservoir walls clean after using the cleaner? Paul Sly:
The varnish that deposits on reservoir walls (often at the top) has access to oxygen in the air, headspace which often allows further polymerisation of the deposits making them hard to remove.
Reservoirs are often low flow and low temperature areas: both factors diminish cleaning. This is common to all cleaners.
Why isn’t my reservoir access hatch clean after using the cleaner? Paul Sly:
The reservoir hatch is usually on the top of the reservoir out of reach of the oil with cleaner in it.
Why didn’t the cleaner clean stagnant areas in my system? Paul Sly:
Cleaning depends on lubricant flow to dissolve and remove the varnish from the area. Minimal flow often means minimal cleaning.
Will the cleaner plug the system’s filters? Paul Sly:
Some alternative cleaners can plug filters, although this depends on varnish and oil chemistry, the type of deposits, and the configuration of the system. It is good practice to have spare filters on hand during cleaning.
Filter differential pressure may increase during cleaning depending on the amount and characteristics of the varnish moved from surfaces into the oil, as larger removed varnish pieces can lodge in the filter increasing pressure. Hard particles (if present) previously stuck in the sticky varnish will also be caught by the filter increasing differential pressure.
VARTECH Industrial System Cleaner has been extensively tested in the field with occasional mild increases in filter differential pressure, but never exceeded alarm limits, even in equipment where other cleaners have done so repeatedly.
Learn more about VARTECH Industrial System Cleaner here: